Enhancing Heat Transfer Efficiency with Modern Heat Exchangers
In the pharmaceutical and chemical industries, heat transfer efficiency plays a crucial role in various processes, including sterilization. Modern heat exchangers have revolutionized the way heat is transferred, leading to improved efficiency and enhanced productivity. This article explores how these advanced heat exchangers contribute to optimizing heat transfer in pharmaceutical and chemical processes, particularly in sterilization procedures.
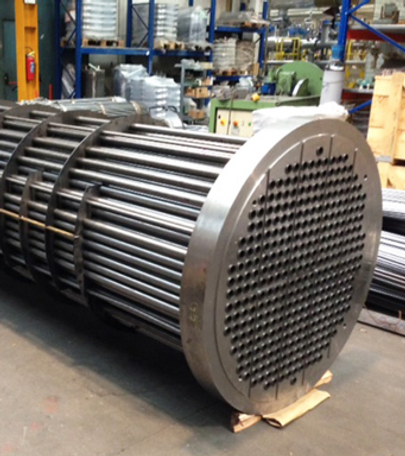
The Importance of Heat Transfer Efficiency in Sterilization Processes
Sterilization is a critical step in the pharmaceutical industry to ensure the safety and efficacy of medical products. It involves the elimination of all microorganisms, including bacteria, viruses, and fungi, from equipment, instruments, and pharmaceutical products. Achieving proper sterilization is vital to prevent contamination and maintain product quality.
Traditional sterilization methods, such as autoclaves, have been widely used in the pharmaceutical industry. However, these methods often face challenges in terms of heat transfer efficiency. Inefficient heat transfer can result in longer sterilization cycles, increased energy consumption, and potential damage to sensitive pharmaceutical products.
Modern Heat Exchangers: Revolutionizing Heat Transfer Efficiency
Modern heat exchangers have emerged as a game-changer in enhancing heat transfer efficiency. These innovative devices utilize advanced technologies and designs to optimize the transfer of heat, leading to significant improvements in sterilization processes. Let’s delve into some key features and benefits of modern heat exchangers:
1. Compact and Efficient Design
Modern heat exchangers are designed to be compact yet highly efficient. Their compact size allows for easy integration into existing pharmaceutical and chemical processes, minimizing space requirements. Additionally, their efficient design ensures maximum heat transfer with minimal energy loss, resulting in reduced operating costs.
2. Enhanced Heat Transfer Surfaces
One of the primary factors contributing to improved heat transfer efficiency is the use of enhanced heat transfer surfaces in modern heat exchangers. These surfaces are designed to increase the contact area between the heat exchanger and the fluid, facilitating better heat transfer. This results in faster sterilization cycles and improved overall productivity.
3. Advanced Fluid Dynamics
Modern heat exchangers incorporate advanced fluid dynamics principles to optimize heat transfer. By carefully controlling the flow patterns and velocities of the fluids, these heat exchangers ensure efficient heat transfer throughout the sterilization process. This leads to uniform temperature distribution and eliminates the risk of hotspots, ensuring thorough sterilization.
4. Intelligent Control Systems
Another notable feature of modern heat exchangers is their intelligent control systems. These systems monitor and regulate various parameters, such as temperature, pressure, and flow rate, to maintain optimal heat transfer conditions. By continuously adapting to changing process requirements, these heat exchangers ensure consistent and reliable sterilization outcomes.
The Impact of Modern Heat Exchangers in the Pharmaceutical Industry
The adoption of modern heat exchangers has had a significant impact on the pharmaceutical industry, particularly in sterilization processes. Some key benefits include:
Improved Product Quality: Enhanced heat transfer efficiency ensures thorough sterilization, minimizing the risk of product contamination and ensuring high-quality pharmaceutical products.
Increased Productivity: Faster sterilization cycles enabled by modern heat exchangers result in improved productivity, allowing pharmaceutical manufacturers to meet growing demands efficiently.
Energy Efficiency: The optimized heat transfer achieved by modern heat exchangers reduces energy consumption, leading to cost savings and a more sustainable approach to sterilization processes.
Process Optimization: The compact design and advanced control systems of modern heat exchangers allow for seamless integration into existing processes, optimizing overall process efficiency.
In conclusion, modern heat exchangers have revolutionized heat transfer efficiency in pharmaceutical and chemical processes, particularly in sterilization procedures. Their compact and efficient design, enhanced heat transfer surfaces, advanced fluid dynamics, and intelligent control systems have significantly improved productivity, product quality, and energy efficiency in the pharmaceutical industry. Embracing these innovative technologies is crucial for pharmaceutical manufacturers aiming to enhance their sterilization processes and stay ahead in a competitive market.
Learn More
For more information on our sustainable practices and equipment offerings, visit our pages on Reactors and Autoclaves, Process Vessel and Tanks, Hydrogenators, Pilot Plant Systems, Distillation Columns, Heat Exchangers and Condensers, and Large Size Pipe and Pipe Fittings.
Check out this Embracing Sustainability: The Eco-Friendly Applications of Exotic Metals
Check out this: Embracing Sustainability: The Eco-Friendly Applications of Exotic Metals
Check out this: The Importance of Material Selection in Chemical Equipment Manufacturing
Check out this: Pioneering the Future of Mining: Extracting Exotic Metals Sustainably
Check out this: The Role of High-Quality Reactors in Pharmaceutical Manufacturing
Check out this: The Future of Exotic Metals in Emerging Applications and Technological Advancements
Check out this: Ensuring Reliability: The Critical Role of Quality Assurance in Large Size Pipe and Pipe Fittings
Check out this: Working with Exotic Metals: Fabrication Techniques and Safety Tips
References: