The Importance of Material Selection in Chemical Equipment Manufacturing
In the realm of chemical equipment manufacturing, the choice of materials plays a crucial role in ensuring the efficiency, safety, and longevity of the equipment. Different processes and chemicals require specific material properties to withstand various operational challenges. This article provides an overview of the materials commonly used in chemical equipment manufacturing and highlights their specific advantages in various applications.
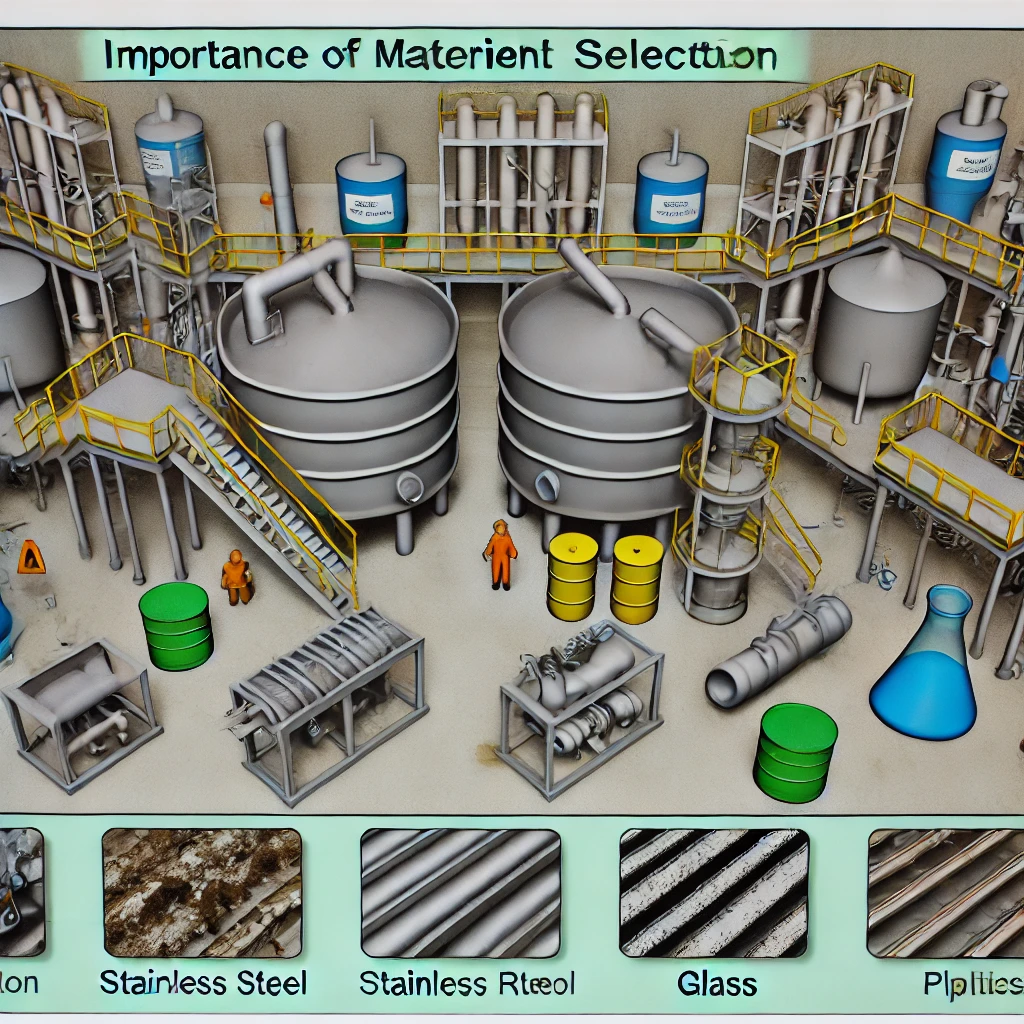
Stainless Steel
Grades: SS304L, SS316L, SS904L, SS310, SS317L- SS304L:
- Advantages: Cost-effective, good general corrosion resistance.
- Applications: Suitable for non-critical applications involving less aggressive chemicals.
- SS316L:
- Advantages: Enhanced resistance to pitting and crevice corrosion, particularly in chloride environments.
- Applications: Ideal for equipment used in pharmaceutical and food industries where hygiene and resistance to chemical exposure are critical.
- SS904L:
- Advantages: Excellent resistance to sulfuric and phosphoric acids.
- Applications: Used in highly corrosive environments, such as acid processing plants.
- SS310:
- Advantages: High-temperature strength and oxidation resistance.
- Applications: Suitable for furnace parts, heat exchangers, and other high-temperature applications.
- SS317L:
- Advantages: Superior resistance to high-temperature oxidation and corrosion.
- Applications: Commonly used in chemical processing and petrochemical industries.
Nickel Alloys
Grades: Inconel-600, Inconel-625, Incoloy-800H/HT, Incoloy-825, Hastelloy C-276, Hastelloy C-22, Nickel 200/201- Inconel-600:
- Advantages: High-temperature strength and excellent oxidation resistance.
- Applications: Suitable for heat-treating equipment and chemical processing.
- Inconel-625:
- Advantages: Outstanding fatigue and thermal-fatigue resistance, oxidation, and corrosion resistance.
- Applications: Ideal for high-stress environments such as marine and aerospace applications.
- Incoloy-800H/HT:
- Advantages: Good strength and excellent resistance to oxidation and carburization in high-temperature environments.
- Applications: Used in heat exchangers, process piping, and equipment in the chemical and petrochemical industries.
- Incoloy-825:
- Advantages: Exceptional resistance to both reducing and oxidizing acids, stress-corrosion cracking, and localized attack.
- Applications: Perfect for equipment exposed to sulfuric acid, phosphoric acid, and other aggressive environments.
- Hastelloy C-276 and C-22:
- Advantages: Superior resistance to a wide range of chemical environments, including strong oxidizers and reducers.
- Applications: Used in chemical processing, pollution control, and waste treatment applications where extreme corrosion resistance is needed.
- Nickel 200/201:
- Advantages: Excellent resistance to caustic alkalis and good thermal, electrical, and magnetostrictive properties.
- Applications: Suitable for chemical processing, electronics, and aerospace industries.
Monel
Grade: Monel-400- Advantages: Excellent corrosion resistance in a wide range of environments, including seawater and steam at high temperatures.
- Applications: Often used in marine and chemical processing equipment, including pumps, valves, and piping systems.
- Corrosion Resistance: Choosing the right material helps prevent corrosion, which can lead to equipment failure and costly downtime. Materials like Hastelloy and Incoloy are specifically designed to withstand harsh chemical environments.
- Temperature Tolerance: High-temperature processes require materials that can maintain their integrity without deforming or degrading. Inconel and SS310 are examples of materials that perform well under high temperatures.
- Mechanical Strength: The mechanical properties of the material, such as tensile strength and hardness, ensure that the equipment can handle the physical stresses during operation. Nickel alloys are known for their excellent mechanical properties.
- Longevity and Durability: Using materials with high resistance to wear and tear increases the lifespan of the equipment, reducing the need for frequent replacements and maintenance.
- Safety: Ensuring that materials can withstand the operational environment reduces the risk of leaks, ruptures, and other failures that could lead to hazardous situations.